46 years - History
-
by Steve Lindsay
History of Lindsay's gravers was originally written in 2000 and still resides
where they were first introduced and sold.
(link)
Click to enlarge photos
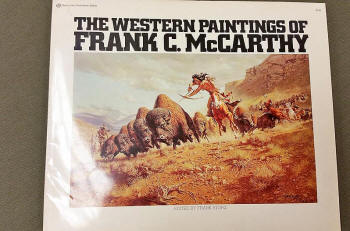
Lindsay
tools are a culmination of 46 years of engraving and tool making by Frank and
Steve Lindsay. In
1975, at the age of 17, Steve began to learn hand engraving with his father
who is a watchmaker and jeweler. Frank became friends with John Rohner and James (Bruce) Meeks. At that time
he purchased John Rohner's
invention called a Gravermeister from John in Boulder Colorado. John's
invention was the world's first pneumatic engraver. John Rohner was a
supporter encouraging Steve to continue learning. Above is a book John
signed in 1977 which was an inspiration to Steve.
In 1977, after graduating from high school,
Steve enrolled in the same Nebraska tech college that his father attended studying watch making.
Steve enrolled
in machine tool and die on the recommendation of John Rohner.
The college and super instructors (i.e. Alan Carter) allowed students to use
the school's machine shop for personal projects in the evening. Taking that
opportunity, Steve created several new hand pieces for the Gravermeister that
he was using. The new hand pieces were palm-sized rather than long. This was
beneficial for smaller, detailed engraving as well as providing improved
control. In 1979, Frank designed an electronic circuit to
oscillate and adjust the speed of a solenoid valve. Air was run through the
valve to produce blow-pulses rather than suction-pulses. Frank made two of
the machines. Steve used the school's machine tools to build
various hand pieces for Frank's adjustable positive pulse generator.
In an interview for the December, 1981 NebraskaLand magazine, Frank's machine
was mentioned and a picture of it can be seen on the back corner of the engraving bench on page five of the article.
NEBRASKAland.pdf
It is the gray box in the
right back corner of the bench. The hand pieces hidden for the article
and from the public for years, and until they were posted on the internet in
2006. At the left is a picture of three
positive pulse gravers made in 1979 for Frank's machine.
Steve found that
the limitation to his father's design and other designs on the market be that
air or electric is that they depend on a spring in the handpiece. The spring
in these designs creates a limited power band. They have an adverse effect of
loss of power, or a complete absence of power when the piston floats, caused
by the pulses giving insufficient time for the spring to return. This is
caused by the frequency of the air or electric pulses being too fast and/or by
too much air pressure or current in each pulse.
Pulse Electromagnet graver
Through the mid and late
90's Steve worked on designing, and attempting to create a new device
that would give an even wider range of power and impact strokes, without
sacrificing the finesse and control my father built into his engraving
machine. The venture led Steve to research to directly using the solenoid as
the handpiece itself using the 555 timer IC circuit from Frank's 555 IC timer
pulse generator machine. The handpiece was an airless electromagnet
graver. The graver worked for the fine engraving, but had
limited power at the top end (or if a heavier spring is used be the same loss
of low end power occurred similar to the air pulse designs giving the same
limited power band).
Problems with the pulse electromagnet engraver were -- The handpiece becomes
hot in your hand. The heavier the engraving done the hotter it gets. Another
problem was magnetism. Watches and magnets do not get a long. Steve's father
is a watchmaker/jeweler and Steve was taught that magnets have no place in a
watch-making shop. Since the graver was an electromagnet it would magnetize
gravers, especially HSS and M42 gravers, as well as other tools it got near it
magnetized.
Finally, by
accident, Steve happened on the current design. The design Steve was
attempting to build then was a two valve system working together as one in a
forward direction, but he found the mechanism ran better backwards. The
challenging aspect was to create an impact pulseless engraver that did not
require either an air pulse or an electric pulse generator taking up space on
the bench, and that would oscillate with the softest whisper of air required
for microscopic engraving shading work and yet be able to muscle out the
background around a scroll design when used with much greater air pressure.
Since 1999 the AirGraver has been working for
Steve's work as well as engravers and
jewelers world wide.
After machine
tool & die school in 1979, Steve continued to engrave by day while working second shift in
the tool room of a Nebraska manufacturer. After regular hours there, he used
their machine tools and continued to refine engraving tools. He also made two
positioning vises for his
father and himself for engraving under. The diamond microscopes Frank used in
his jewelry store. In 1980 after the tools were refined
and efficient, Steve quit the factory machine tool job and began full time engraving. Another friend of
Frank's, Lynton McKenzie, recommended Steve attend the knife makers' guild show
in Kansas City in 1980.
He
took the top side of this
linked 9mm Browning to the show. Lynton was
at the show and took him from table to table to introduce him to knife makers and
his collectors. Knife markers such as Buster Warenski, Steve Johnson, Steve
Hoel, Ron Lake, Jim Hardenbrook and Jim Ence were at the show. From
those introductions, knife makers and collectors gave Steve engraving jobs. (some can be seen at
www.LindsayEngraving.com ). For
the next few years, Frank made more improved hand pieces with his lathes and
milling machines that Steve then used for his engravings. In 1984 or
1985 James Meeks came by to say hello and visit. He was working on his second book then and brought along
many white plastic plates. He explained the surface was white but when cut into, the lines
showed black. He had engraved them with various scrolls and example designs.
He explained he was engraving this plastic because the engraving would
photograph well for the book. After that visit Don
Glaser Sr. called and said
that Meeks really enjoyed seeing my palm sized powered graver. It was an awkward phone call
because Steve did not show Meeks his hand piece during his visit. Steve
did receive a phone call while Meeks was visiting and he was left alone at the
bench for a short time. He must have
found the hand piece. It was interesting because after that Mr. Glaser
brought out a new smaller hand piece that had a plastic mushroom handle on the
butt, unlike
the hand pieces they were making that were long and straight with
a
handle midway rather than at the end. It did not matter since Steve was
not in the tool business at that time, but only engraving for collectors.
In 1987 Frank and Steve did some engraving projects together. They produced five engraved folding knives.
Steve drew the outlines of the knife designs and Frank made and set the diamonds, and
Steve then engraved them. Frank's knives
had hidden watch screws and wedges and would come apart allowing the inside
surfaces as well as the outside ones to be engraved. The five pieces
were called Lindsay-Lindsay. The Japanese knife engraving market was strong
then and several of them went to customers and dealers in Japan selling for as
much as $40,000. Later the owner of the #5 piece contacted Steve with
the news that he had a terminal illness and wanted to sell and was asking
$110,000. It was offered for sale on the
LindsayEngraving.com
site and was resold.
Lynton Mckenzie
and Steve engraved a SCI Safari
Club International rifle project together. David Miller was the maker, Lynton
engraved the rifle and Steve did the accessories and a Steve Hoel folding knife
that were cased with the rifle. The piece sold at auction for
$210,000. There is a photo of the accessories
at link. Click
the photo there to enlarge,
link.
Lynton had also been engraving Gene Clark's
watches. When Lynton became sick in early 1998 he recommended to Gene that
Steve engrave
them. Steve engraved three of Gene's watches. An improved design
was completed while working on the second one.
That second one was auctioned at Sotherby's and sold for $62,500.
Lindsayengraving.com/Clark.htm
Through the years the tool continued to be improved.
There is a video
of one of Gene's watch faces being engraved in the above link.
Various AirGraver designs.
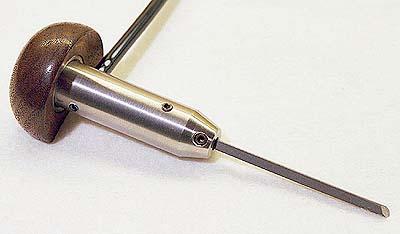
1. The self oscillation
pulsefree AirGraver piston principle was patented. It can operate with very little air
pressure or air volume. In fact, by simply blowing in it. Even attached to a toy balloon, the tool will idle. Instead of a
spring for the return or impact stroke, the device uses air pressure for both
directions. As a result, the piston always stays balanced and low or high air
pressures can be used without one side overpowering the other causing the piston
to float, which can occur with the spring-pulse designs. The patented idle of
the new design prevents jumps that sometimes occur with spring-pulse designs.
The stroke length and speed adjustment is in the bore of tool. Adjustment is
made by removing the graver and adjusting the screw at the bottom of the tool
hole.
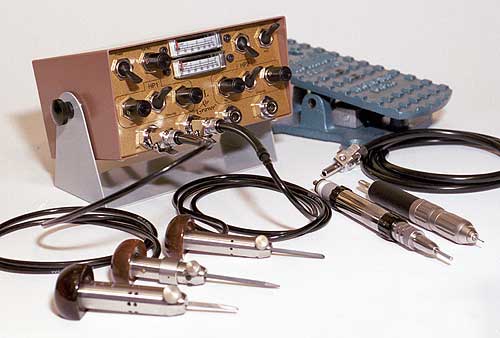
2. A multiple controller box is shown above. Since this box required a lot of work to
manufacture, it was replaced by using either a simple toggle-routing valve on the current foot controller setup, or quick disconnects. This development allows as many
hand pieces and rotaries as needed to be operated at the same time.
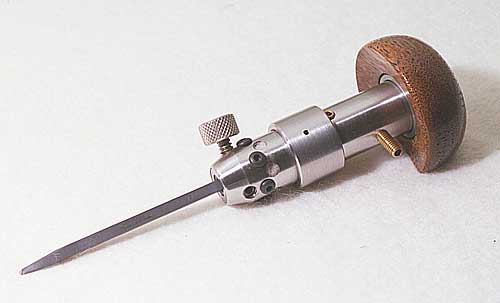
3. One way to move the length-of-stroke adjustment to the outside of the hand
piece was the ring pictured above. Only one of these was made as a prototype and
it was patented when the snap on/off handle was patented. The tool worked nicely,
but it was difficult to make and assemble because of all the small internal
parts.
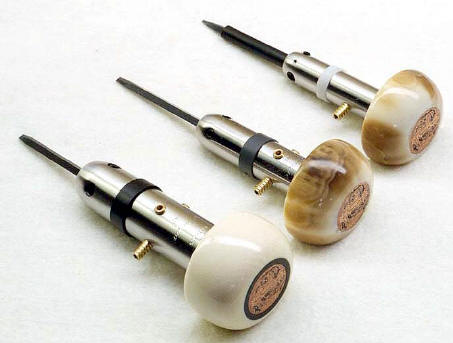
4. In the design shown above, stroke adjustment was still in the tool hole, but
the addition of the black rings around the body made it possible to adjust the
exhaust by turning the ring. When a stroke adjustment was made, the exhaust
could also be tuned to make them run even better.
The stroke adjustment on the tools makes one hand piece as versatile as a
variety of different-sized hand pieces.
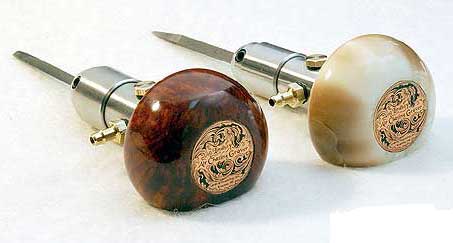
5. Away to adjust the
stroke by moving the nose in and out with a ring around the body, while
simultaneously adjusting (tuning) the exhaust was an additional patent.
Synchronizing the two made the tool run well throughout the stroke range,
without having to adjust one and then the other. The ring works in a manner
similar to focusing a lens on a camera. Because of the way the nose is held in
place, the impacts are isolated to the nose and graver shank. This leads to less
vibration to the body during impacting, and provides significantly more power
when needed.
The stroke adjustment is similar to gears in a car and makes the tool perform like numerous handpieces
in one. First gear is good for shading and fifth gear is good for background. If
thinking about it this way, the old pulse machines similar to my father's machine has
one gear.
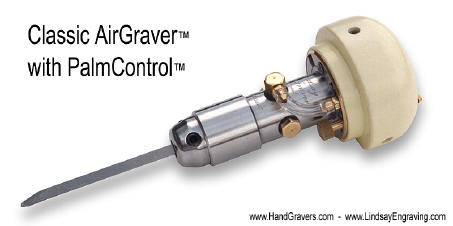
6. The development of the PalmControl meant the
elimination of the foot pedal. I noticed that while engraving with a foot pedal,
engravers also vary the pressure used to hold the graver point in a cut.
Depending on the depth, engravers vary the amount of palm pressure. This idea
was built upon by making a handle that would automatically respond to the palm
pressure to operate the throttle. The concept for the PalmControl was: why do we
have to duplicate with a foot pedal what our hand is already doing? It was also patented. The legal enforceable claims of the patent protect a hand push pressure activated power tool used in the
hand engraving and jewelry fields.